In the near future, as permanent communities are planned for construction on the moon, the demand for water transportation to and from the lunar surface becomes important. To optimize efficiency and cost-effectiveness, a groundbreaking approach is being undertaken. NASA is utilizing a Lunar Flashlight to orbit the moon and identify significant ice deposits on the dark sides of the moon (lunar south pole) for water extraction.
Our objective is to provide the capabilities to keep the Lunar Flashlight mission in lunar orbit and maintain orbit for the duration of its research mission.
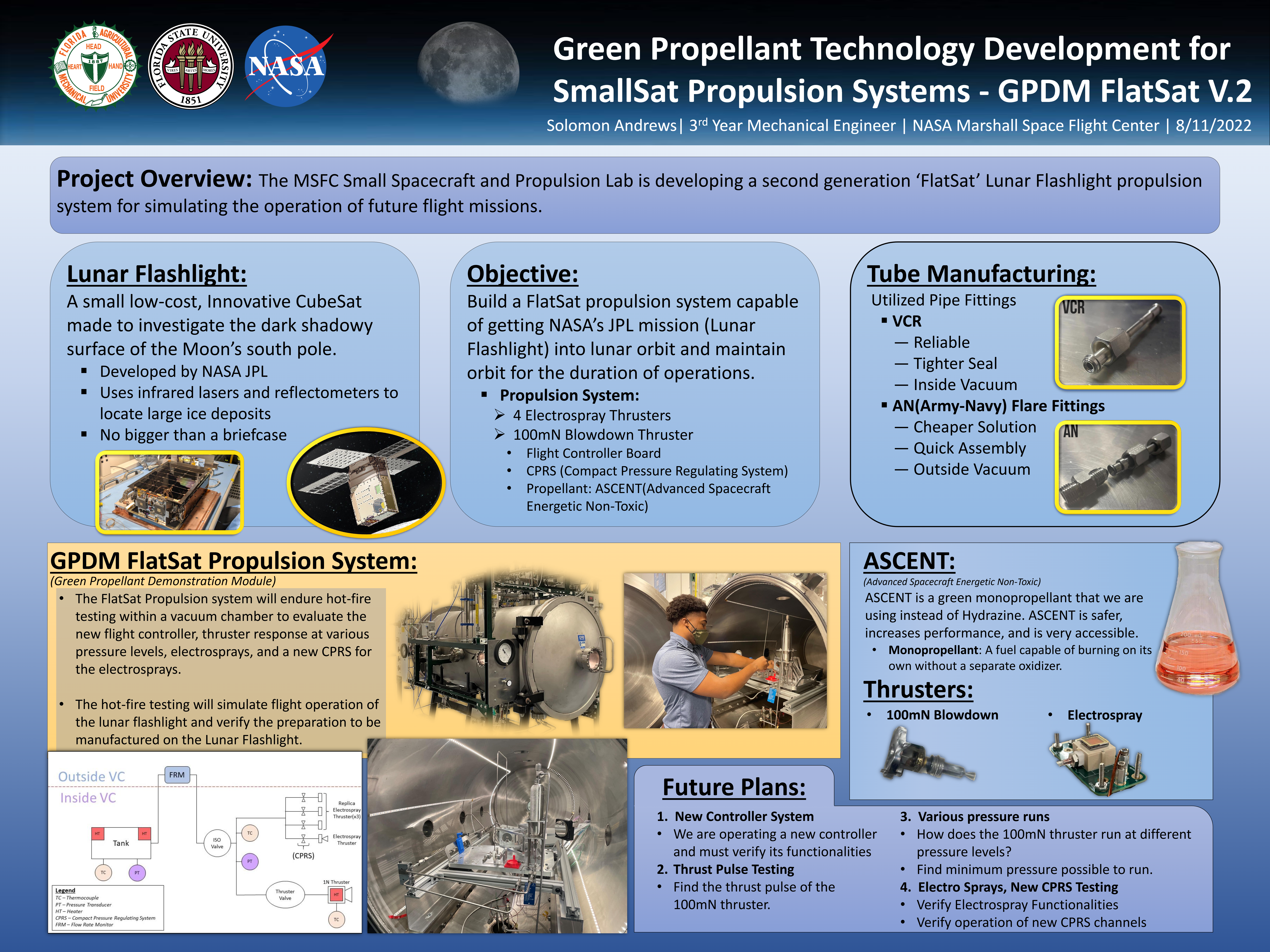
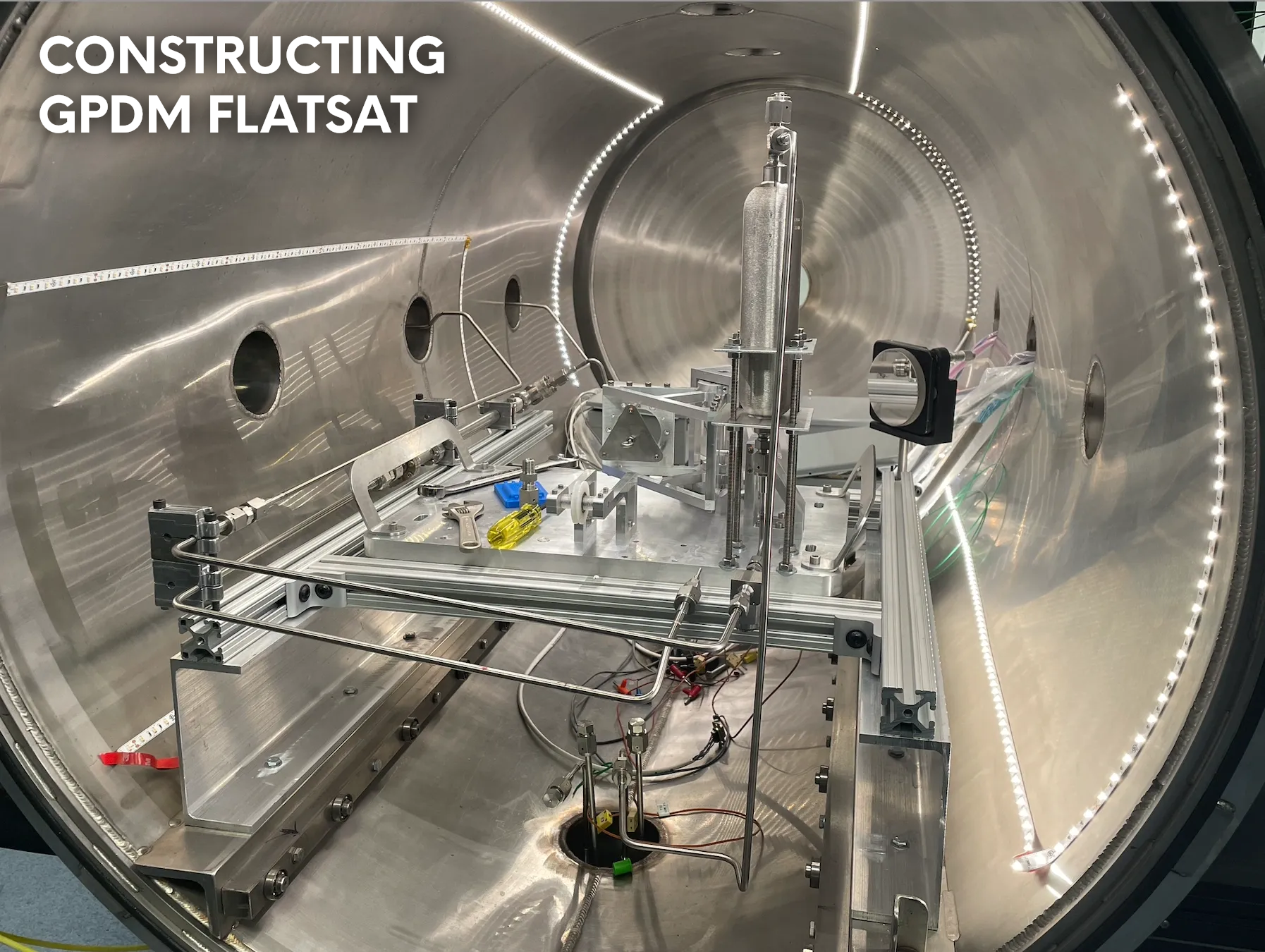
The FlatSat propulsion system serves as a crucial testing phase for the propulsion system before its integration into the Lunar Flashlight. This platform offers complete openness and accessibility for any necessary modifications, allowing for comprehensive assessment of hardware performance under operational conditions.
Our FlatSat design comprises five thrusters enclosed within a vacuum chamber. This includes one 100mN blowdown thruster and four electrospray thrusters.
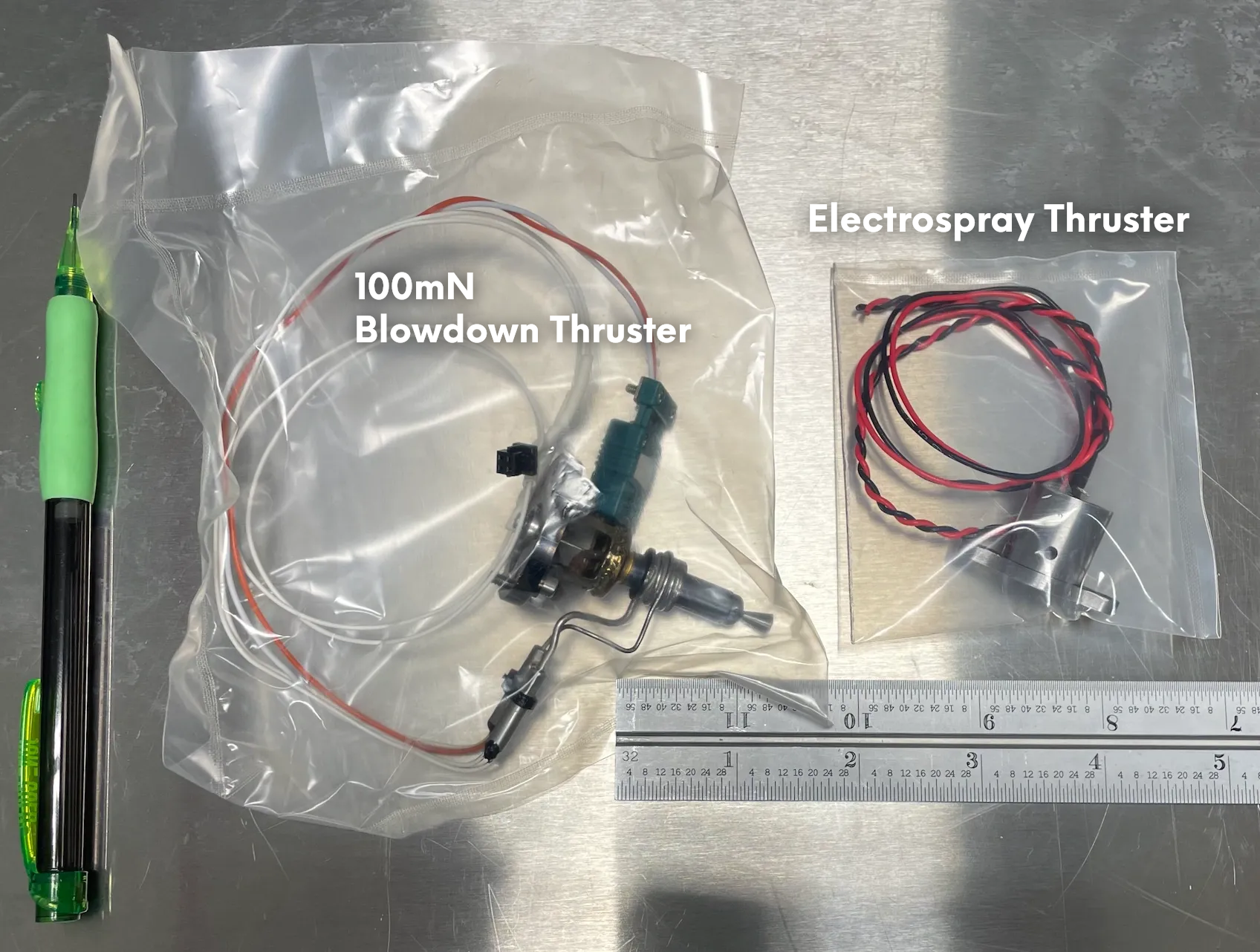
The propulsion system's tube manufacturing incorporates various components such as regulators, pressure transducers, flow meters, and flight controllers, all instrumental in verifying the integrity of our designed solution during test operations.
These tests encompass evaluations of the new flight controller, the 100mN thruster pulse, system responses across varying pressure levels, the compact pressure regulating system for electrosprays, and more.
The manufacturing of the operational FlatSat design has been completed and assembled within the Lunar Flashlight. On Sunday, December 11 at 2:38 a.m. (ET), SpaceX successfully launched the Lunar Flashlight to a lunar transfer orbit from Space Launch Complex 40 (SLC-40) at Cape Canaveral Space Force Station in Florida.
This marked the Falcon 9's fifth launch and landing.